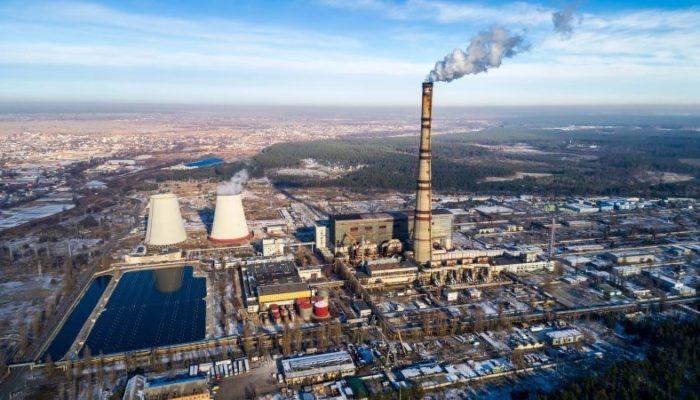
Although you may not realise it, waste and the circular economy is an important topic for many geoscientists. Our consumption drives the need for resources and sustainable resource extraction, while disposing and reducing this waste requires a wide range of expertise and impacts the environments in which many scientists undertake their research. On a more personal level, understanding what happens to the things that we buy (and then dispose of) is a good reminder to consume more mindfully, particularly during this time of year when we may be consuming more than normal. This month’s GeoPolicy blog post, written by Daniel Parvaz, zooms into the EU’s end of waste criteria and secondary raw material policies using Incinerator Bottom Ash (IBA) as an example.
Waste Incineration
Though not the first stage in the Waste Hierarchy for a circular economy, municipal solid waste incineration is an attractive alternative to landfilling. This is both due to the generally large public opposition to new landfill sites and the potential to recover both energy and secondary raw materials such as Incinerator Bottom Ash (IBA) (the residue of the burned waste) and the metals it contains. There are over 500 municipal waste incinerators in Europe, producing roughly 19 million tons of IBA annually, of which 10 – 12 % of this mass is metal. This corresponds to almost 2 million tons of metal that can be recovered and recycled, worth up to €180 million. The other 85 % of the IBA mass is the mineral fraction which includes ceramics, glass, stone and slag that forms during the incineration.
Recycling Incinerator Bottom Ash (IBA) products
Once the IBA is crushed and metals liberated, they can be sorted using industry standard mineral processing systems and sorters. Metals can be sold as mixed scrap but the problem of the residual material remains. Typically, this was landfilled, however with the drive towards 100% recycling and sustainability, several end-uses are available.
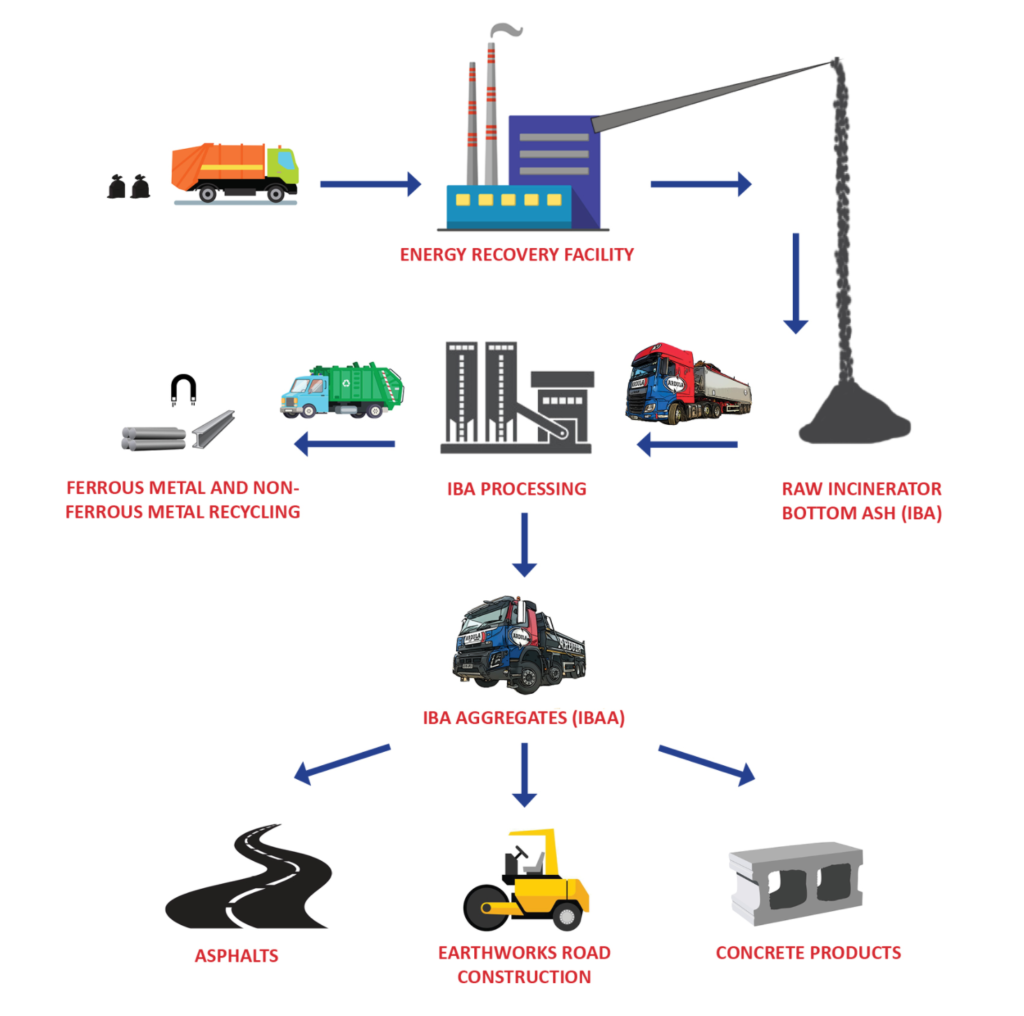
Origin and fate of incinerator bottom ash. From Ardula.
The most common use for incinerator bottom ash aggregate is as road infilling or pipe bedding. This is traditionally done with dry treated IBA after metal extraction. IBA aggregate is also commonly used to make light building materials such as cinder or breeze blocks (‘breeze’ being and old term for these ashes). However, despite recovering as much metal as possible before using the material for construction, a relatively high metal content may still remain. Not only does this have financial implications, but it could also have environmental and health consequences as a result of the metals leaching into the surrounding soil and water. Before IBA can be used in construction, leaching tests need to be undertaken to ensure that harmful compounds cannot reach the water supply.
Policy implications
There is no uniform regulation for IBA utilisation at the EU level, so countries have independently developed their own rules for utilisation. The EU’s Waste Framework Directive has created end of waste criteria that help to define when waste should be given the status of a secondary raw material. This status aims to incentivise recycling, provide a framework for legal security when using such a material, protect the environment, and promote the commercialisation of a waste material and subsequent economic benefits. Secondary raw material status may be obtained at EU or national levels. At an EU level, this status has already been given to certain scrap metals and glass cullet. IBA currently doesn’t meet these ‘end of waste’ criteria that would enable it to have wider usage, according to environmental restrictions.
Municipal waste, and the bottom ash it becomes, contains all kinds of material, from metals to discarded food, not all of which is fit to go back into the ground. Most countries specify that IBA needs to meet specific leaching criteria before it can be used in infrastructure to minimise the risk of contamination or pollution of groundwater. The elements in question, threshold concentrations and even test methods are country specific, with no regulated limits or procedures set by the EU: Switzerland, for example, has stricter laws and classes IBA aggregate as ‘waste’ meaning it cannot be used as a construction aggregate regardless of its composition, while other countries have more lenient criteria to allow the 100% recycling of IBA.
The properties of a bottom ash derived aggregate can also impact the lifespan of the infrastructure that it is used in. If, for example, native metals or oxides are used as an aggregate in concrete, these may slowly oxidise and adversely impact its strength.
Looking forward: reducing landfill and increasing the use of IBA
Metal content
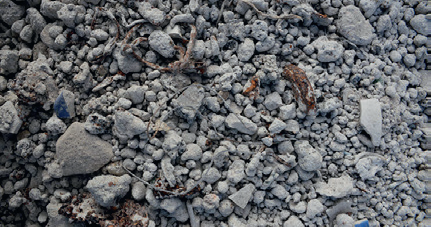
Untreated incinerator bottom ash. Photo Credit: Alexander Weh.
Every effort must be made to reduce metal content of IBA before use in construction. Currently there are no restrictions on the amount of metal that can be contained within material to be used as IBA aggregate, only on the soluble phases. The high metal content means that IBA aggregate is in undesirable in cement and is susceptible to oxidation in the form of unbound gravel. Additionally, metals such as aluminium that emit hydrogen as they oxidise should be strictly regulated as they can result in a build-up of H2 gas, which has resulted in several explosions. Until there are restrictions on the aluminium content, concrete using IBA aggregate should only be used outdoors or in a well-ventilated area.
There are a number of methods for reducing metal content including through electric pulse fragmentation (currently being undertaken by the Swiss company Selfrag), literally ‘washing’ the IBA to remove readily soluble compounds, or more extensive leaching and solvent extraction to recover metals.
Strength classification
The lack of strength criterion for concretes using recycled (incinerator bottom ash) aggregates is another barrier to their uptake. The lack of research into this field means that civil engineers have little information work with. With pressing deadlines, would you use unknown, untested material, or resort to traditional aggregates with little variation which can be relied upon? Their low uptake in the construction industry is something of a Catch-22: The recycled aggregates are of low value as they can’t be used without strength data, and generating strength data is of little interest due to the low value of the aggregate. The generation and exploitation of this data could be a step change in the circularity of the construction industry.
Incentivisation
As usual, things come down to money. In this way policy makers can either choose the carrot or the stick, appropriately rewarding or punishing builders who do or don’t use recycled aggregate. Often, it’s better to reward than chastise, and this is best done through financial incentive. Builders meeting targets for recycled concrete aggregates use might be given ‘Green credits’, similar to Renewable Energy Certificates, or some other form of reward. A method used by the Norwegian, and undoubtedly other governments, is that of placing emphasis on CO2 footprint in tenders. That means that the cheapest option is not necessarily the one the award goes to, but the one with the least environmental impact. In this way, construction companies are incentivised to source recycled materials wherever possible, which will hopefully drive the research into a proper strength classification of IBA aggregate concrete. Naturally, this requires the inclination of government to place environment over revenue and would not occur in every nation.
In any case, as the middle class grows the world over, trash generation is something that will never go away. To move forwards to a more sustainable economy, we need to find ways to reduce the amount of material going to landfill, re-use what we can, and recycle metals and other aggregates.
About the Author
Daniel Parvaz is the Director of Lightning Machines mineral processing consultancy. He received his PhD in Earth Resources from the Camborne School of Mines in the UK. After Camborne Daniel spent several years at SELFRAG developing and optimising applications for their pulsed power process, before leaving to found Lightning Machines in 2019. His research interests include: the application of electric pulse treatment to improving energy efficiency in mining; recycling of waste into raw materials; ore deposit formation; materials policy and marketing, and he maintains a research blog on his website.