As geoscientists in Europe, we should consider ourselves to be very lucky to have a rich architectural heritage. The first insights we gain about the geology of an area can be read in beautiful historic buildings. For centuries, construction and architecture have been driven by two constraints: adapt to the local environment, and use locally available materials. Heritage buildings thus represent valuable information for a geoscientist (see this lecture at “La Sorbonne” on environment and heritage, ref1). There’s no doubt about the subsurface materials when observing the architectural heritage: black buildings around the Eifel (Germany, ref2, ref3) sign the presence of nearby lava flows (Fig 1a-b) whereas blocks of greenish sandstones in the constructions that scatter across the Swiss Alpine foreland basin signify the “Lower freshwater Molasse” (Fig 1c-d, ref4). As a sedimentologist, my favourites are the fantastic churches and monuments constructed from the famous rose “Buntsandstein sandstones” (Fig 1e-f). The thrill of recognizing sedimentary structures in these building materials often surpasses my excitement seeing gargoyles and other architectural details.
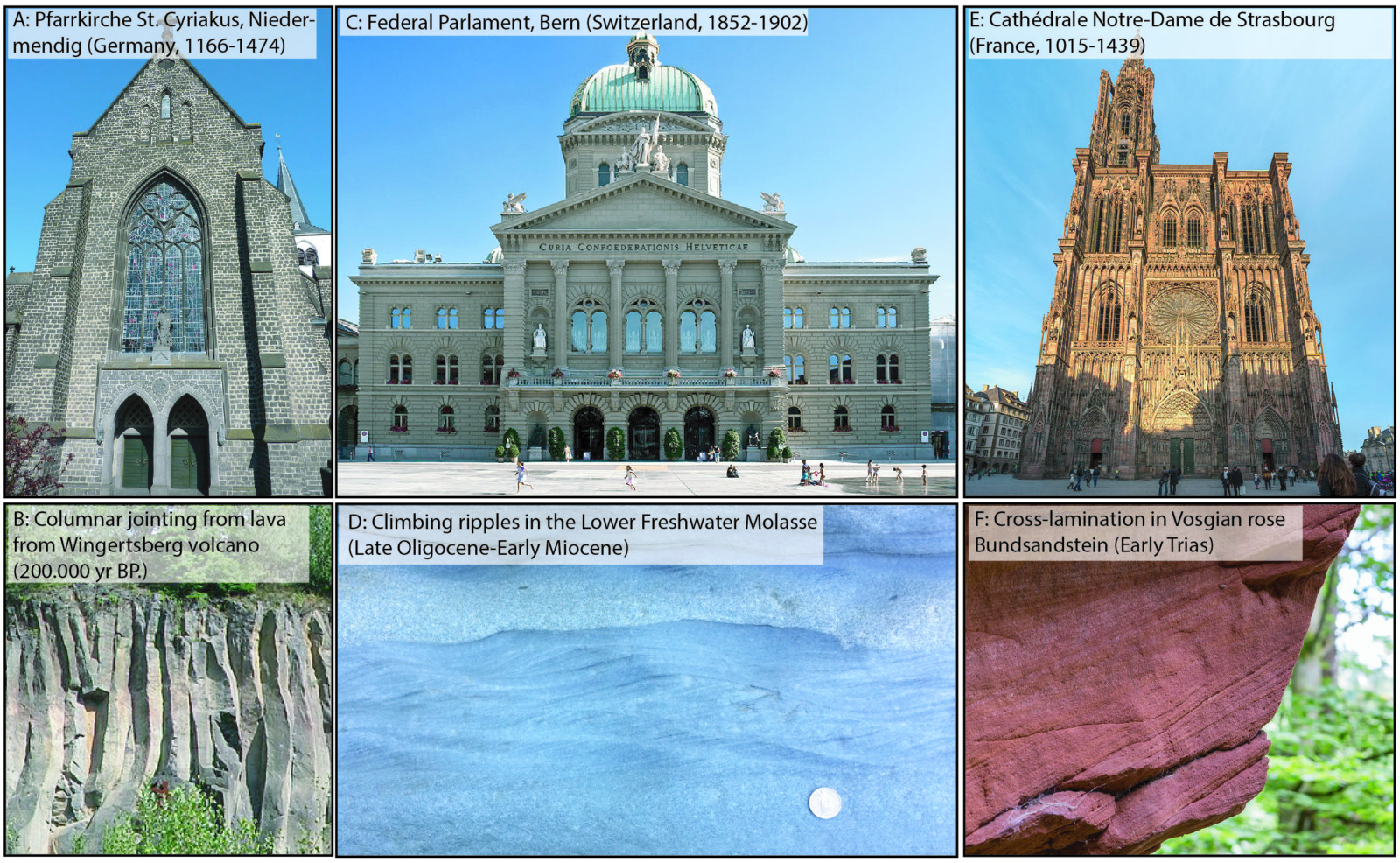
Historic buildings and the rock composing them. A) The “Pfarrkirche St. Cyriakus”, in Niedermendig (Germany) constructed from 1166 to 1474, and B) the rock formation composing it -a lava flow erupted around 200.000 years ago from the Wingertsberg volcano. C) The Swiss Federal Parliament in Bern (Switzerland), constructed from 1852 to 1902 is made of block from D) the “Lower Fresh Water Molasse” formed in the Early Miocene. Note trains of climbing ripples. E) The “Cathédrale Notre-Dame de Strasbourg” (France) erected and modified from 1015 to 1439 is composed of F) Vosgian Rose “Buntsandstein” from the Early Trias. Credit: A-B-C-E-F: Wikipedia, D: G.A. Douillet
Timber houses and loam
Here, I’d like to focus on timber-framed houses (Fig 2). These buildings generally follow a common structure: a wooden skeleton (timber-frame) for the structural stability and a composite filling based on a raw earth binder (“loam“, i.e. a mixture of sand, silt and clay, ref5) mixed with an aggregate or reinforcement of mineral or plant origin (Fig 3). Such houses can be found virtually everywhere where loess (fine-grained aeolian deposits related to the last glaciation, see also this previous SSP-blogpost) or fine-grained-alluvium (unconsolidated terrestrial sediment deposited by water) was the easiest material to extract. Worldwide, loess covers 10% of the land surface (ref6, ref7), a third of the human population lives in a raw-earth construction (see Niroumand et al. 2013) with examples all over the world (e.g. http://eartharchitecture.org/). Timber-houses are constructed in many styles over large parts of Western Europe, with local variations that inform on the local environmental constraints (Fig 2). Interestingly, for seismologists, it seems that the timber-structure contains a majority of vertical and horizontal framing in aseismic areas (e.g. Fig 2a in French Normandy, ref8), whereas diagonal cross-bracing can be the sign for historic earthquakes (e.g. Fig 2b around Basel, where a large earthquake destroyed the city in 1356, and the last noticeable one in the area was a 5.2 in 2004 -in Waldkirch). The filling of loam mixture also holds information, for climatologists: in regions with a hard winter, a light mixture of loam with a reinforcement of straw is preferred for its insulating power (e.g. “torchis” or “wattle-and-daub” technique in the Rhine valley). In warmer areas or zones with high day-night temperature changes, the filling tends to be made of compacted “rammed-earth” with an aggregate of gravel, which ensures a good thermal mass (e.g. “Pisé” technique around the Southern French Alps).
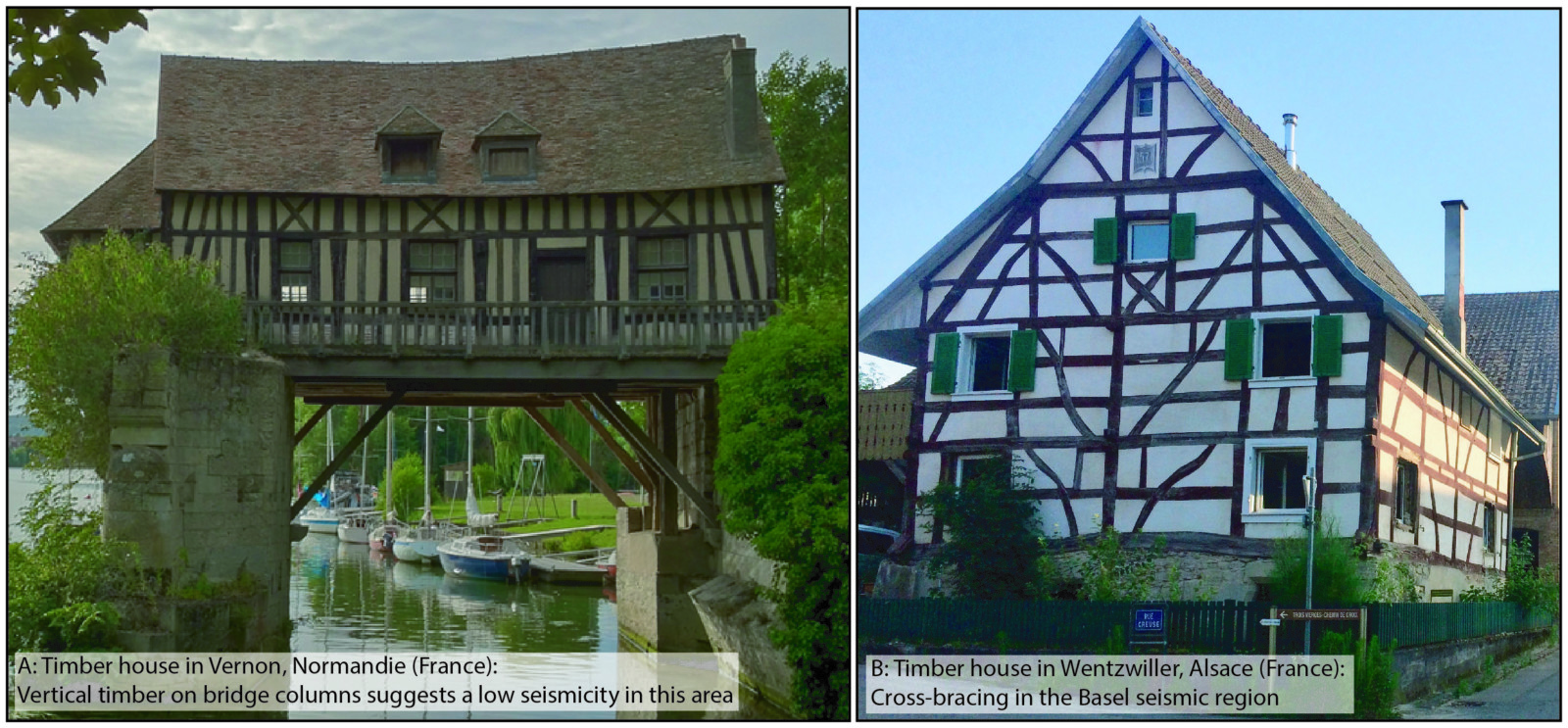
Timber-framed houses in France. A) The house “Le vieux moulin” (16th century) in “Normandie”, with framing mainly containing vertical and horizontal timber is built in a non-seismic zone. B) A house from 1571 in Wentzwiller (Alsace): the cross-bracings of the timber structure are optimized for the seismic region around Basel. Credit: A: Wikipedia B: G.A. Douillet
Loam, straw, hemp
The most common plant-based reinforcement used in the composite loam mixture is straw (since at least 6.000 years); which, for most of Europe, is available locally (Fig 3a). Hemp mortar was discovered in bridge abutments (Merovingian bridges) in France built in the 6th century. The hemp core or “Shiv” has a high silica content which allows it to bind well with lime or clays, forming a “Hempcrete” (Fig 3c). This property is unique to hemp among all natural fibres. Nowadays, hemp is making a huge come-back in construction and offers many environmental advantages: it grows fast, needs almost no water and no pesticides. The fibres can be used for textiles, offering a very good alternative to the highly resource-consuming cotton or nylon. Hemp has been used since the neolithic and used to be a widespread grown plant exploited for many uses (e.g. for cordage, clothing, paper, food, biofuels, bioplastics…) until the middle of the 19th century. Unfortunately, the hemp industry slowed to a near-halt in profit of cotton and nylon in the 1930s. The rediscovery of hemp use for construction occurred in France in 1986, and nowadays benefits from detailed good-practice rules (ref9). The French hemp production peaked at 176.000 ha cultivated in the 19th century and decreased to a minimum of 700 ha in the 1960s. However, production is increasing again reaching 16.500 ha in 2018 (+ 2300% since the 1960s!).
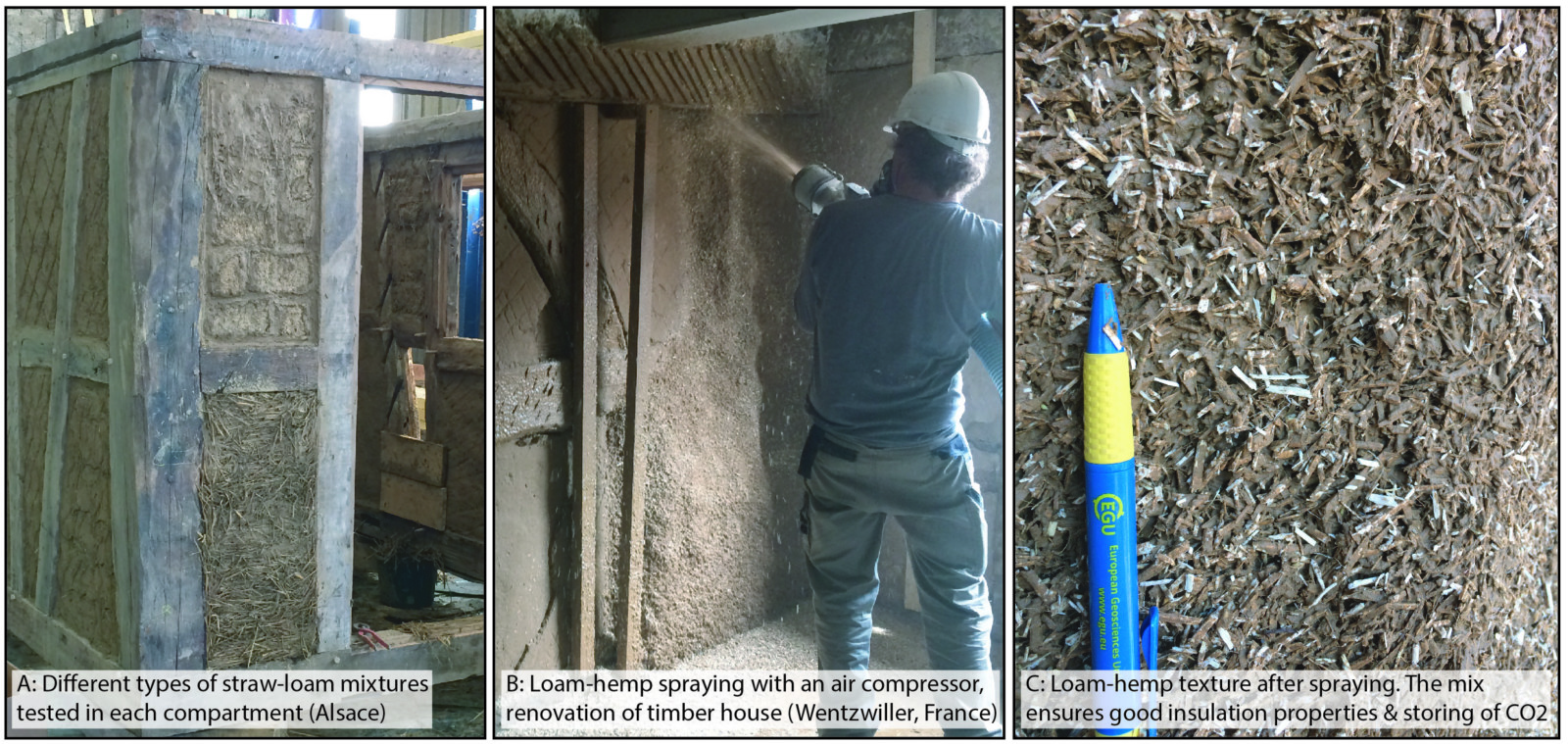
Modern loam construction. A) Different loam-straw mixtures applied in this timber-frame during a Workshop from the “Association pour la Sauvegarde de la Maison Alsacienne- ASMA” in 2019. B) Application of a loam-hemp insulation inside the timber-framed house in Fig 2B by spraying -a full scale test with ecosphere-habitat.com-. C) Texture of the sprayed loam-hemp mixture. Credit: G.A. Douillet
The industrial construction catastrophe
Construction techniques have however evolved drastically since the industrial revolution. The development of the famous “Portland cement” (ref10), steel, and oil-based products have changed our construction norms. But the generalization of their use to virtually every construction site is an error and regression, in my opinion. The advent of these techniques came with a cost: the construction sector is currently sucking up 25 to 50% of the total energy consumption in Europe (ref11). The “clinker” (the bulk of a Portland cement) is a mixture of ca. 80% limestone and 20% clays (aluminosilicates), which need to be extracted, crushed, transported, and heated to ca. 1450ºC before becoming a cement. Cement processing is responsible for 8% of the world CO2 emissions (ref12), which is astonishing! If the cement industry were a country, it would be the third largest emitter in the world. Lafarge-Holcim, the French-Swiss world-leader of cement production, is said to cause more CO2 emissions than oil companies such as Total or BP.
Cement is then mixed with sand to make concrete, posing another problem: did you know that sand has been exploited so much that it becomes a scarce resource in several parts of the world? The illegal commerce of sand drives mafias and geopolitical instability in several places (see e.g. the incontrovertible documentary “Sand Wars”, ref13). More recently, products derived from organic chemistry have become huge for insulation and other uses: epoxy additives in concretes, modern plastic foams (e.g. polystyrene) for insulation, and PVC (polyvinyl chloride), to name a few. Whereas concretes, metallic structures and plastic products can be fantastic materials in some situations, do we need a systematic use of them? No.
A huge potential for the future
Working toward increasing the use of timber-framed houses coupled to loam and hemp shiv as building materials has thus a huge potential for our future. Every square meter of wood stored in a building contains 0.9 tons of CO2 that have been naturally taken from the atmosphere and will be stored for (hopefully) several hundred years (20 m3 of wood for an individual timber-house = 18 tons CO2). The same applies for a mix of loam and hemp used for the filling: optimizing insulation for the heating period (counting 40 cm thick walls), it takes about 90 m3 for an individual house, and with 100 kg of hemp per m3, it does store approx. 16.5 tons of CO2. The loam should be available at the construction site and not need any transport. As a comparison, an average European produces around 4-10 tons CO2 a year. It is time to re-discover that construction can store CO2 by using biodegradable and locally produced materials as an alternative to releasing CO2 and consuming scarce resources. And whatever pragmatism could suggest, this is not yet the norm, and I believe that there is an urgent need to communicate this with constructors and consumers.
Existing projects
Happily, some people, groups and projects are aiming at refining ancient techniques of loam constructions and bringing them back in our modern world. The research lab “CraTerre” in Grenoble (France) works on every aspect of raw earth construction including an inventory of methods around the world (ref14). In Switzerland, the association “IG-lehm” groups artisans and architects that work with loam (ref15). One emblematic example is the “Via-Felsenau” living project in Bern (ref16), a construction of loam and wood hosting 35 people, constructed in the early 90s by architect Arwed Junginger (ref17). As one of the residents there, I can testify that the living comfort in a raw-earth building is superior to modern concrete ones (in terms of apparent temperature, air quality, and acoustic quality). In Germany, it is the Dachverband-Lehm that groups people around loam constructions. In France, the scene becomes more and more active, citing just a few events of the last month: the design competition on “Alsatian timber house of the 21st century” (ref18, ref19) and several international congresses on “bio-based buildings” (ref20, ref21). AsTerre is an association that is federating professionals of raw Earth construction. The technique of loam-straw (Fig 3A) and loam-hemp (Fig 3B-C) construction is also booming. In particular, the recent method of spraying a loam and hemp mix with an air-compressor (Fig 3B-C) offers great insulation characteristics, as well as efficient and fast application (>15 m3 applied per day with 2 persons, ref22) that could be applied to large-scale industrial use. My experience renovating an old Alsatian timber-house using the splattering loam-hemp method (with “Eco Sphere Habitat“, Fig 3B-C, ref23) was efficient, cost-friendly, safe, and easy to apply. Above all, it’s a very comfortable insulating material for living and a joy to know it produced no waste.
To conclude, I find there to be a huge issue with our modern construction methods, and inspiring ourselves from the past offers incredibly adapted solutions for the future. These solutions involve locally grown plant materials and loam, a sediment. I am sure that some of us in the Stratigraphy-Sedimentology-Paleontology community could bring our expertise in that subject to support and further develop the use of these heritage methods in architecture.
References
- ref1: http://vof.paris-sorbonne.fr/fr/index/licence-XA/sciences-humaines-et-sociales-SHS/licence-histoire-de-l-art-et-archeologie-program-laha1-211/l2-histoire-de-l-art-et-archeologie-subprogram-lahab2-14/ue1-methodologie-L3AA01MU/environnement-et-patrimoine-L3AA51PG.html
- ref2: http://www.osteifel-aktiv.de/41527/74901.html
- ref3: Schmincke, H.-U. (n.d.). The Quaternary Volcanic Fields of the East and West Eifel (Germany). Mantle Plumes, 241–322. doi:10.1007/978-3-540-68046-8_8
- ref4: Schlunegger, F., Matter, A., Burbank, D. W., Leu, W., Mange, M., & Matyas, J. (1997). Sedimentary sequences, seismofacies and evolution of depositional systems of the Oligo/Miocene Lower Freshwater Molasse Group, Switzerland. Basin Research, 9(1), 1-26.
- ref5: https://en.wikipedia.org/wiki/Loam
- ref6: Vasiljević, Djordjije A., Slobodan B. Marković, Thomas A. Hose, Ian Smalley, Ken O’Hara-Dhand, Biljana Basarin, Tin Lukić, and Miroslav D. Vujičić. “Loess towards (geo) tourism–proposed application on loess in Vojvodina region (north Serbia).” Acta Geographica Slovenica 51, no. 2 (2011): 391-406. https://ojs.zrc-sazu.si/ags/article/viewFile/1328/1091
- ref7: Haase, D., Fink, J., Haase, G., Ruske, R., Pécsi, M., Richter, H., … Jäger, K.-D. (2007). Loess in Europe—its spatial distribution based on a European Loess Map, scale 1:2,500,000. Quaternary Science Reviews, 26(9-10), 1301–1312. doi:10.1016/j.quascirev.2007.02.003
- ref8: https://fr.wikipedia.org/wiki/Le_Vieux-Moulin_(Vernon)
- ref9: Construire en chanvre: https://www.construire-en-chanvre.fr/missions
- ref10: https://en.wikipedia.org/wiki/Portland_cement
- ref11: Assessment of sustainable construction practices. Sattar Sattary. 38th International Conference of Architectural Science Association ANZAScA“Contexts of architecture”,Launceston, Tasmania, 10–12 November 2004. http://anzasca.net/wp-content/uploads/2014/08/ANZAScA2004_Sattary.pdf
- ref12: https://www.bbc.com/news/science-environment-46455844
- ref13: Sand wars movie: http://sand-wars.com/
- ref14: http://www.craterre.org/recherche/
- ref15: https://www.iglehm.ch/
- ref16: https://www.baubio.ch/verein/zeitschrift/artikel/via-felsenau-baubiologischer-lehmbau-der-pionierzeit/
- ref17: http://www.aab-architekten.ch/
- ref18: https://www.youtube.com/watch?v=zGO4z7_ydk4
- ref19: http://www.strasbourg.archi.fr/la-maison-alsacienne-du-21%C3%A8me-si%C3%A8cle
- ref20: http://toc.proceedings.com/33854webtoc.pdf
- ref21: https://www.construction21.org/community/pg/pages/view/42836/
- ref22: https://www.ecopertica.com/mise-en-oeuvre/terre-chanvre/
- ref23: http://www.ecosphere-habitat.com/
Pingback: GeoLog | Looking back at the EGU blogs in 2019: a competition - GeoLog